
However, it also reduces overall output efficiency and therefore there is an additional incentive for raising operating temperatures and pressures in order to maintain the same amount of saleable energy per power station.Īn example of the materials used in these state-of-the- art projects is illustrated in Fig. The inclusion of CO2 capture and storage technology for fossil fuel power plants represents a significant advance in terms of combating CO2. 1 Government agencies such as the Department of Energy in the USA are funding large, ambitious projects for the development of ultra- supercritical (USC) power plant designed to operate at 760° C and conversions from supercritical to USC opera- tions at 700° C have been carried out in Japan.2Retrofitting of existing plant is a popular option for improving output with minimal investment, since existing fittings can be used. Figure 1 illustrates how CO2 emissions vary with thermal efficiency. Increasingly, the demand for efficiency is linked to efforts to reduce CO2 emissions, in order to meet environmental obligations and minimise any form of punitive environ- mental tax. The target operating temperature for these steels is 650uC, with a common target design life of 100 000 h.
POWER FACTORY 15 CRACK DRIVER
Improved thermal efficiency of power plant has been the main driver for the development of ferritic–martensitic 9– 12%Cr creep-resistant steels that are also commonly known as creep strength enhanced ferritic (CSEF) steels.
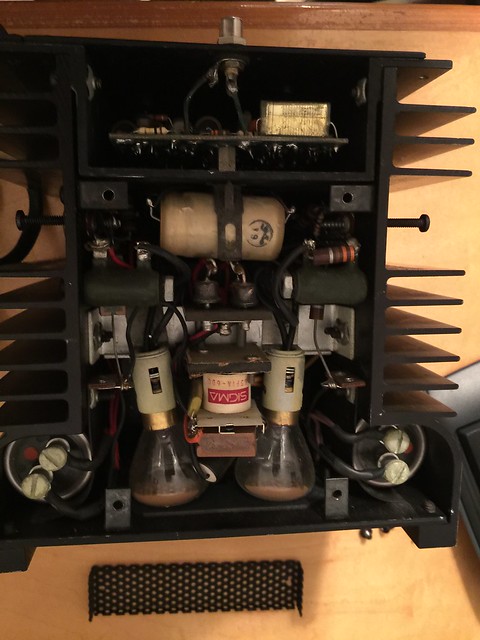
This review aims to serve as an update, drawing selectively on some of the vast amount of literature that has been published over the last 30 years.
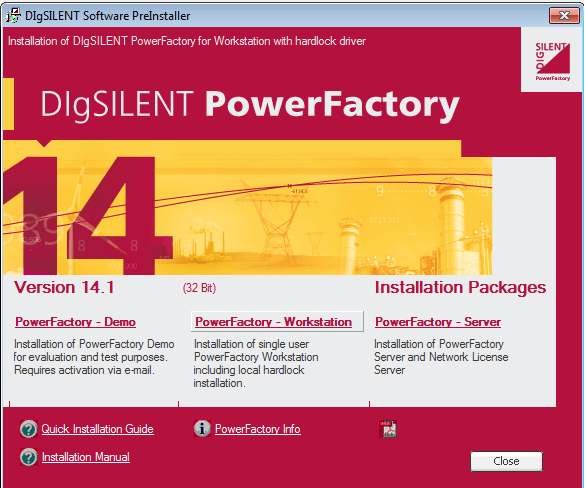
The subject of type IV cracking has been an area of active research interest. Unfortunately, the newer steels suffer from reduced cross-weld creep strength due to type IV cracking to a greater degree in the temperature range of operation expected of them, and thus many failures by this mechanism have occurred. Despite the occurrence of type IV cracking experienced in lower alloy predecessors, successor alloys have been introduced and widely used with insufficient consideration given to the consequences of welding them.
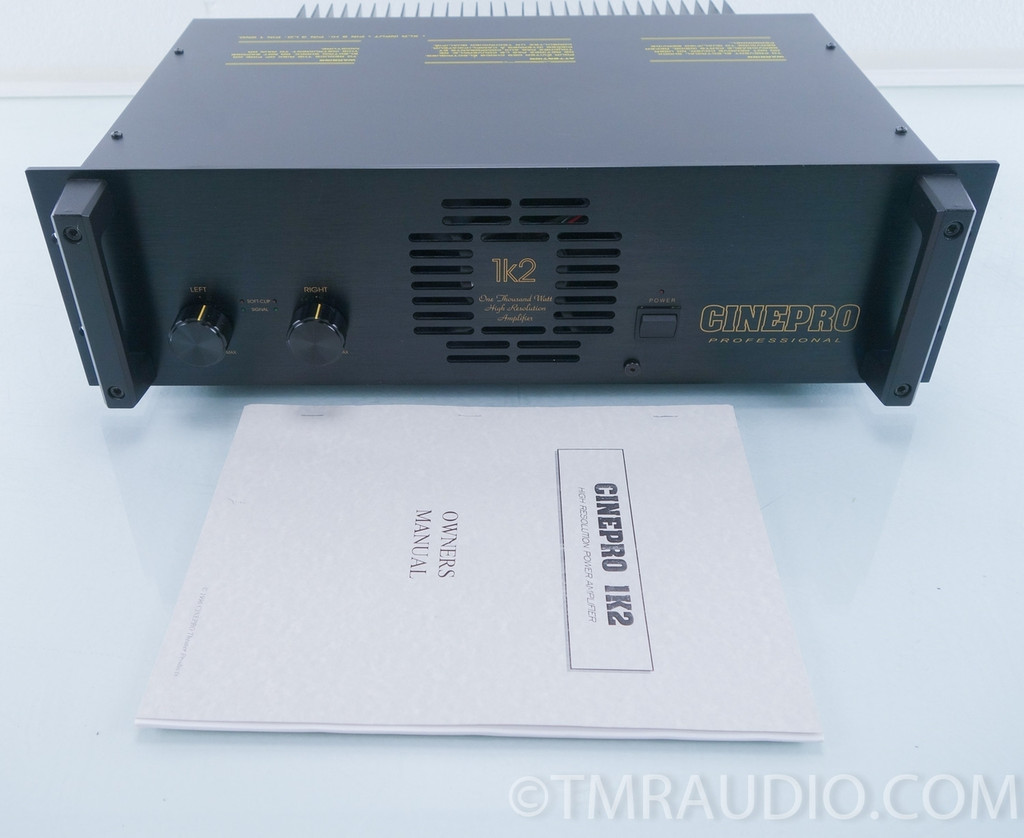
This type of cracking occurs in the intercritical or fine grain region of the heated affected zone via a creep mechanism, and results in fractures with relatively little total cross-weld strain. The high temperature conditions that these steels operate under in fossil fuelled power stations induce type IV cracking. They are also finding use in high temperature process plant within the oil and gas sector, and are being considered for use in generation IV nuclear designs.

Good progress has been made in developing such steels, which are being used particularly in the wrought form as tubes and pipes for fossil fuelled power stations. The improvement of thermal efficiency of power plants has provided the incentive for the development of the martensitic–ferritic 9–12%Cr creep-resistant steels. Review of Type IV Cracking of Weldments in 9-12%Cr Creep Strength Enhanced Ferritic Steels
